ゴム加工の基礎知識
ゴム加工を徹底解説!成形、切削、接着加工からゴム種別性質まで
ゴム加工とは
ゴム加工とは目的の性質や形状を持ったゴム製品を作ることで、主には成形加工、切削加工等が用いられます。 ゴムにはどのような形状の作り方があるのか、どのような性質を持たせることが出来るのか、このページではゴムの性質から種類、成形加工や切削加工の詳細まで、詳しく解説します。
- 1.ゴムの性質について
- 2.ゴムと金属とプラスチックの違い
- 3.ゴム加工の精度(公差)について
- 4.ゴム加工の種類
- 5.性質が全く違う!把握すべきゴムの種類
- 5-1.NR(天然ゴム)
- 5-2.BR(ブタジエンゴム)
- 5-3.SBR(スチレンブタジエンゴム)
- 5-4.NBR(アクリロニトリルゴム)
- 5-5.ACM(アクリルゴム)
- 5-6.Si(シリコンゴム)
- 5-7.CR(クロロプレンゴム)
- 5-8.EPDM(エチレンプロピレンゴム)
- 5-9.FKM(フッ素ゴム)
- 5-10.IIR(ブチルゴム)
- 6.ゴムの加工不良と対策
- 7.ゴム加工会社の選び方
- 8.まとめ
ゴムの性質について
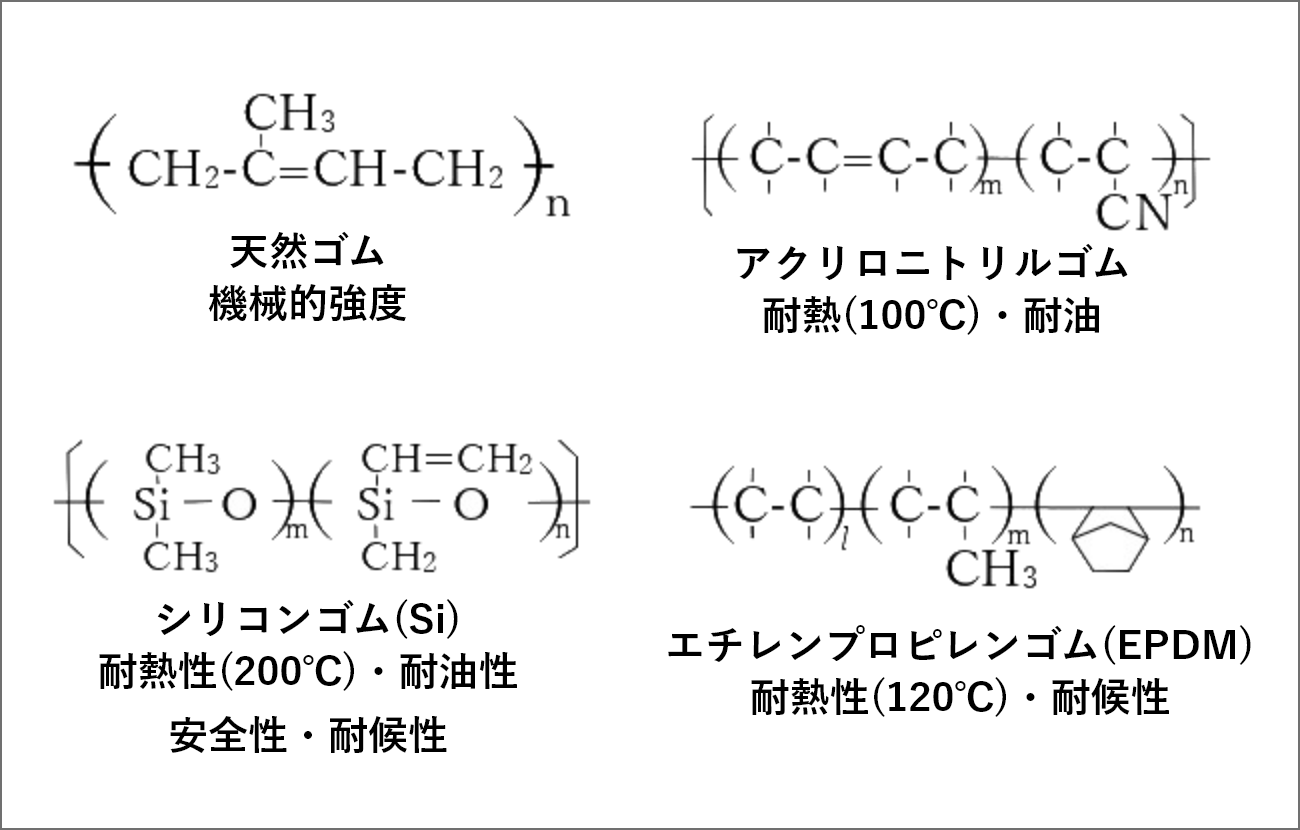
ゴム加工というと、形状を作ることばかりを重視されがちですが、ゴムの性質を把握しておくことも非常に重要です。 例えば、天然ゴムは機械的強度が非常に高いため、自動車の防振ゴムなど大荷重がかかる場所に適しています。しかし、天然ゴムは耐油性がないため、オイルシールのパッキンに使用してしまうと、ドロドロに溶けて製品不良となってしまうでしょう。オイルシールならば耐油性のあるNBRやシリコンゴムを選択しなければなりません。 高温環境での耐油性が必要ならばシリコンゴムやフッ素ゴムですが、常温ならば安価なNBRで十分です。 電線のハーネスなど日が当たる場所では耐候性のあるEPDMが適しています。もしもハーネスに天然ゴムやNBRを使用すると、分子中に二重結合があるため、日光で硬化しボロボロになります。 このように、ゴムの性質を把握することはゴム加工において非常に重要です。 このページでは切削加工やゴム成型などの形状加工についてはもちろん、ゴムの種類ごとの用途や性質も含めて解説します。
ゴムと金属とプラスチックの違い
ゴムと金属とプラスチックの違いは、以下の表の通りです。
ゴム | 金属 | プラスチック | |
---|---|---|---|
形状 |
変形する
|
しない | しない |
劣化 | |||
導電性 | なし | あり | なし |
加工性 | |||
コスト | |||
シール性 | |||
比重 | |||
衝撃吸収 | |||
リサイクル性 | |||
汚染性 |
この中でも特にゴム独特の特長は、
- 変形すること
- 衝撃吸収性があること
- シール性があること
それから、ゴム独特のデメリットとして、ゴムの種類によっては汚染性(色移り)が発生するという事があります。
変形する性質について
ゴムは変形するために、加工する際の精度が出にくいです。また、気温によって膨張と収縮が発生しやすいです。 したがって、金属ほどの寸法精度を出すことは難しいでしょう。±0.5~mm程度の誤差は許容する必要があります。ただし、多少サイズが違っても変形するので、組み込み、はめ込みなどを行うことが出来るという長所もあります。
衝撃吸収性について
ゴムには衝撃吸収性があります。そのため、自動車の防振ゴムや建物の免震ゴムなどに使用されています。衝撃吸収には動倍率と、tanδという指標が用いられます。動倍率が低いとスーパーボールのように跳ね返りがよく、高いと跳ね返りは悪いです。動倍率が低いゴムはバネをイメージすると理解しやすいでしょう。一方、tanδは振動を抑制する指標です。tanδが高いと、衝撃が来てもそれを感じにくくなります。低反発のマットレスを想像すると良いでしょう。ゴム配合においては、ポリマーの比率が高まるほど動倍率が高まります。特に天然ゴムは動倍率が高いです。天然ゴムのポリマーは、触った感触でもブルンブルンとしているので何となく動倍率が高いのは測定しなくても感触で分かります。tanδは、ブチルゴムが高いです。ブチルゴムはポリマーからベチャっとした感触なので、こちらも何となく触っただけでtanδが高そうな察しがつきます。加硫後、製品化したゴムでもブチルゴムはやはりベタリとした感触があります。自動車部品の防振ゴム製品の分野では動倍率が低く、tanδが高いゴム材料が求められます。
シール性について
ゴムは変形し、復元性があるために、シール性があります。パッキンやガスケットにはゴムが用いられます。止水パッキン、油のパッキンは柔らかく復元性のあるゴムが用いられます。 パッキンやガスケットを使う場合には、ゴム材料の選定が必要不可欠です。ゴム材料自体に極性があるかどうかを把握しましょう。止水パッキンならば、EPDM等の無極性のゴム。耐油パッキンならばNBRやACMなどの極性があるゴムを使う必要があります。
汚染性(色移り)について
古い輪ゴムを使おうとして、ひっぱるとプチッと切れた経験は誰しもがあると思います。これはゴムの酸化劣化によるものです。ゴムの種類により、酸化して弱くなるゴムとそうでないゴムがあります。例えば天然ゴムやNBRなど分子中に二重結合があるゴムは空気中のオゾンにより酸化しやすいです。そのため、これらのゴムには酸化防止剤が添加されます。しかし酸化防止剤は汚染性があるものが多く、ゴムと何かが密着するとその酸化防止剤の色が密着相手に色移りしてしまうことがあります。タイヤを長い間置いていた床は、変色しているのを見たことがあるかと思いますが、まさにその現象です。プラスチックや金属には基本的に汚染性はありませんが、ゴムは種類によって汚染性がありますので、注意が必要です。
ゴムの特長と製品例
ゴムの特長 | 製品例 |
---|---|
シール性 | パッキン、オイルシール、ガスケット、液送チューブ、電子レンジ、タッパー、エアホース、タイヤ、ホース、防水ゴム |
衝撃吸収性 | 防振ゴム、橋の橋脚ゴム、タイヤ |
電気絶縁性 | ハーネス、グロメット、電線被覆材 |
弾力 | ボール、防振ゴム |
ゴム加工の精度(公差)について
一般的にゴム加工品は素材の特性上、寸法公差が生じやすいため、金属加工のように厳密な精度で仕上げることは不可能です。
また、寸法公差の検査方法や検査官によって数値が変わることも多いため、ゴム製品には下記のような寸法公差表が参考とされることがあります。
どうしても精度が必要な場合は、金型を使用する、成形条件(素材、硬度など)を整えることが必要です。
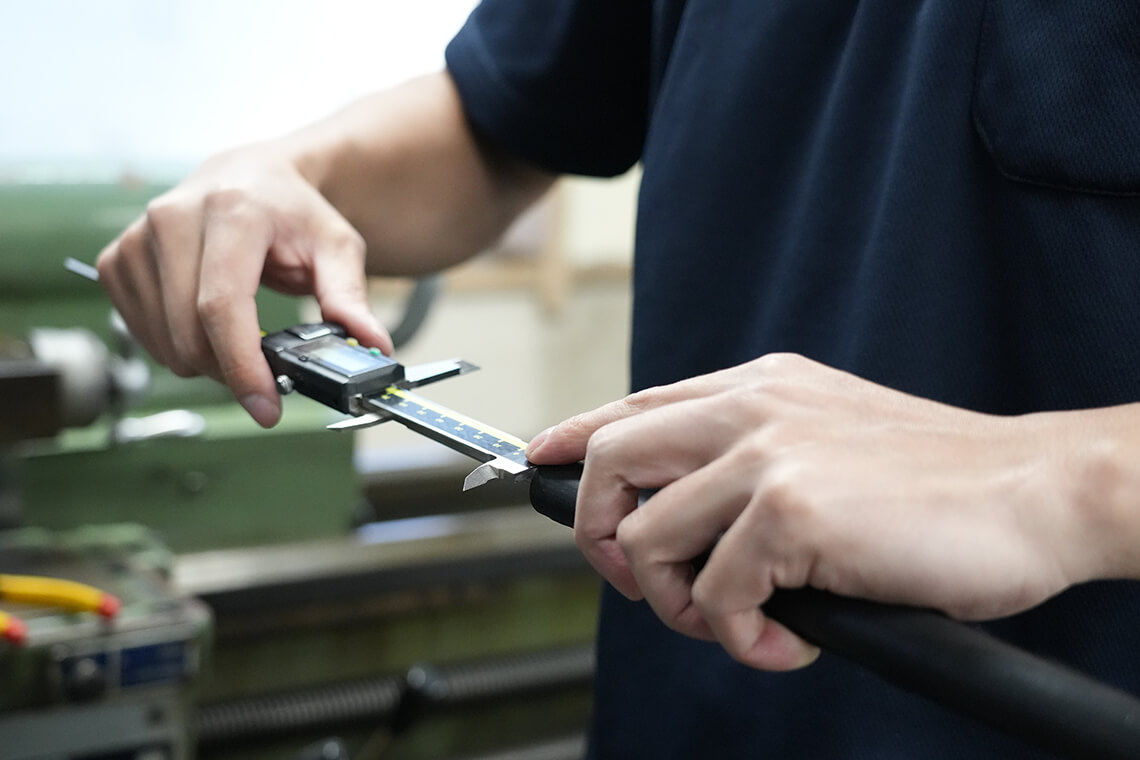
工業用ゴム製品寸法公差表(VDI:ドイツ技術者協会)
寸法区分 | 1級(精級) | 2級(精級) | 3級(精級) |
---|---|---|---|
0.3以上3未満 | ±0.2 | ±0.3 | ±0.4 |
3〜6 | ±0.2 | ±0.4 | ±0.5 |
6〜10 | ±0.3 | ±0.5 | ±0.6 |
10〜18 | ±0.3 | ±0.6 | ±0.8 |
18〜30 | ±0.4 | ±0.8 | ±1.0 |
30〜50 | ±0.5 | ±1.0 | ±1.5 |
50〜80 | ±0.6 | ±1.2 | ±2.0 |
80〜120 | ±0.7 | ±1.4 | ±2.5 |
120〜180 | ±0.8 | ±1.6 | ±3.0 |
180〜250 | ±1.0 | ±2.0 | ±4.0 |
250〜315 | ±1.2 | ±2.5 | ±5.0 |
315〜400 | ±1.5 | ±3.0 | ±6.0 |
400〜500 | ±1.8 | ±3.5 | ±7.0 |
500以上 | ±0.4% | ±0.8% | ±1.5% |
ゴム加工の種類
ゴム加工には大きく分けて、切削加工、成型加工、接着(ライニング)加工、塗装の4種類があります。 特に切削加工と成型加工はどちらにするかを迷うケースが多いため、まずはこの二種類を比較します。
結論から言うと、少量生産・納期重視なら切削加工、大量生産ならば成形加工をお勧めいたします。詳しくは下の表をご覧ください。
ゴムの金型成形と切削加工の違い
ゴム金型成形 | ゴム切削加工 | |
---|---|---|
初期コスト | 形状や取り個数によって金額に大きな差がある 簡易的な形状で1個取りだと10万円弱 高額なものだと200万〜300万 |
|
ランニングコスト | ||
納期 | リードタイムが長くなる |
|
量産にむけた試作 | 本番と近いものが作れる |
ができない早い、安価 |
量産 | ||
寸法精度 | ||
複雑形状の製品 | ||
面粗精度 |
切削加工は治具があればあらゆる形状に加工出来るため、初期コストが安価です。しかし、大量生産となると一つ一つの切削に時間がかかるため、量産性は低くなります。 一方、成形加工は金型を製作する必要があるため、初期コストが高くなり、金型製作の納期もかかります。ただし、一度金型を作ってしまえば、短時間で大量に製品を量産することが可能です。また、精密さは金型成形に分があります。寸法精度や複雑形状の製造、面粗精度いずれも金型の方が良好です。これらの違いをご自身の状況に当てはめて、加工法を選択されると良いでしょう。
切削加工
切削加工は、既存のゴムの塊やシートを刃物や切削工具で目的の形に切って形作っていく加工方法です。切削加工と一言に言っても、様々な加工方法があります。
- 旋盤加工
- 材料を回転させて、固定した工具を当てて削ります。
- フライス加工
- 工具を回転させ、固定した材料を当てて削ります。
- ろくろ加工
- 陶芸のろくろのように、ゴムの塊を回転させて工具を当てて削り取ります。
- 打ち抜き加工
- クッキーの型抜きのように、ゴムに型抜き刃物を当てて切り取ります。
- ウォータージェット加工
- 水圧でゴムを切ります。ゴムの変形がすくなく、熱も発生しないため、綺麗に切ることが出来ます。
- スリッター加工
- ゴムをスリットのように細い板に切っていく加工法です。
- プロッタ加工
- 精密機械に形状をプログラムし、機械がその形通りに刃物でゴムを切って加工します。
- 研磨加工
- ゴムを切り取った後の断面の凸凹やバリを研磨することで綺麗にします。
成形加工
成形加工は、ゴムを金型でプレスして形を作る加工方法です。金型に入れる前のゴムは、ゴム材料と呼ばれます。ゴム材料は、食べる前の板ガムのような状態で、伸縮性がありません。伸ばしても縮まず、伸びっぱなしで、弾力も、強度もありません。 ゴム材料を加熱し、加硫(硫黄との化学反応を起こすこと)することで、我々がよく知っているゴムらしい弾力のある状態に化学変化し、実用が可能となります。 加硫反応は室温でもゆっくり進みますが、実際の生産現場では150度~200度に加熱して化学反応をさせていきます。そのため、成形に使う金型は温度が150度~200度と非常に高温になります。 (成形作業者は火傷や、夏は熱中症に気をつけなければなりません。大変な作業です。) 一度金型を作ってしまえば簡単に何度も同じ形を作れるため、切削に比べ大量生産に向いています。
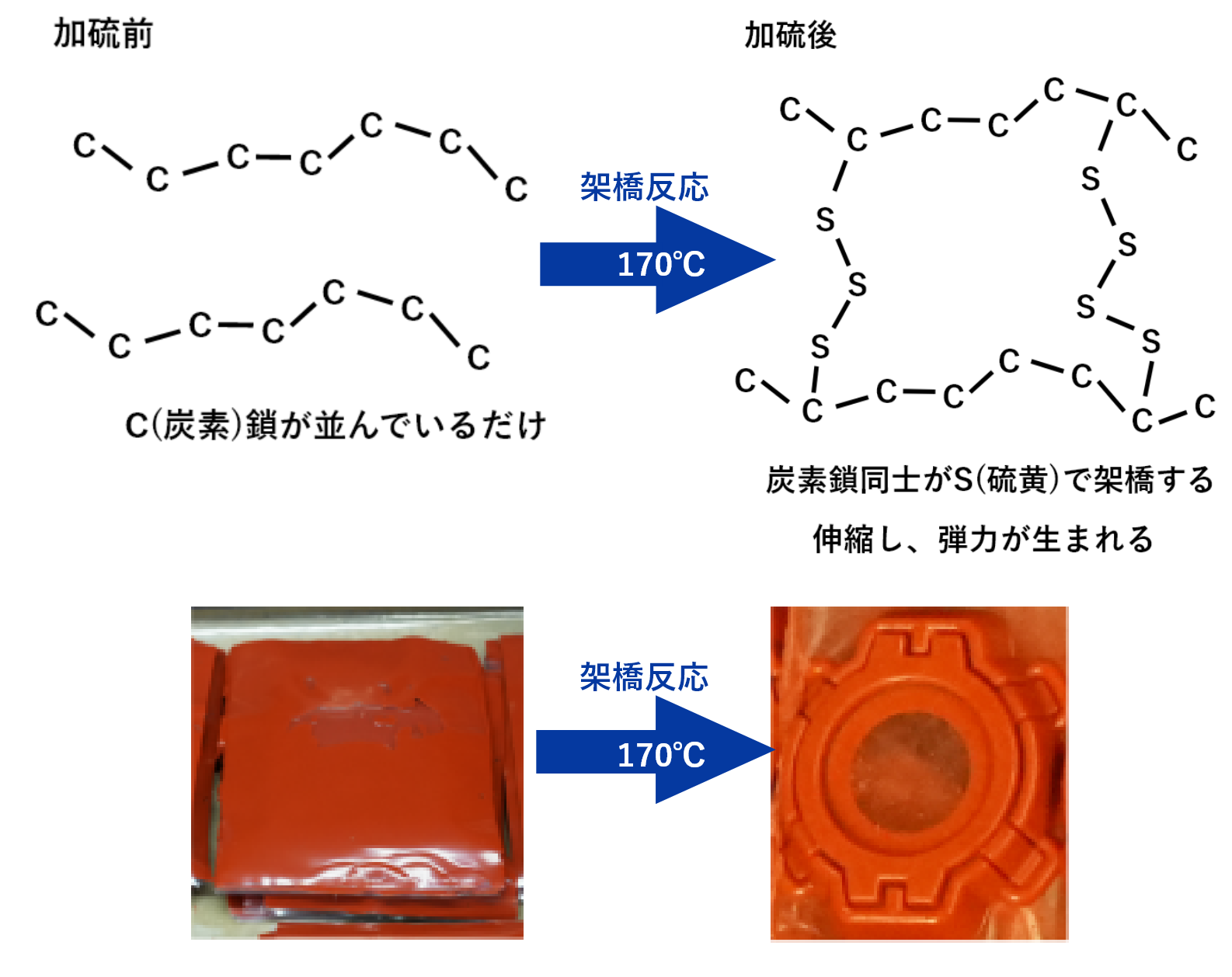
ゴム配合について
ゴム材料にはゴムそのものだけでなくカーボンブラック、炭酸カルシウムなど補強材や、生産性を上げるための加工助剤や、可塑剤、加硫促進剤や硫黄など様々な薬品が混ぜられています。この配合により、耐熱性、機械的強度、加工性が大きく変わります。この配合技術はゴム関係各社の秘伝となっています。
ちなみに、多くの工業用ゴムが黒いのはカーボンブラックが入っているからです。カーボンブラックを配合することでゴムの機械的強度(引張強度、引き裂き強度、耐摩耗性など)は劇的に上がります。オレンジや白などのゴムはカーボンブラックの代わりにシリカが入っています。シリカもゴムの強度を上げてくれますが、カーボンブラックに比べるとかなり弱いです。黒くないゴムは、強度はそこまで高くないと思ってよいでしょう。
成形加工の種類について
プレス成形
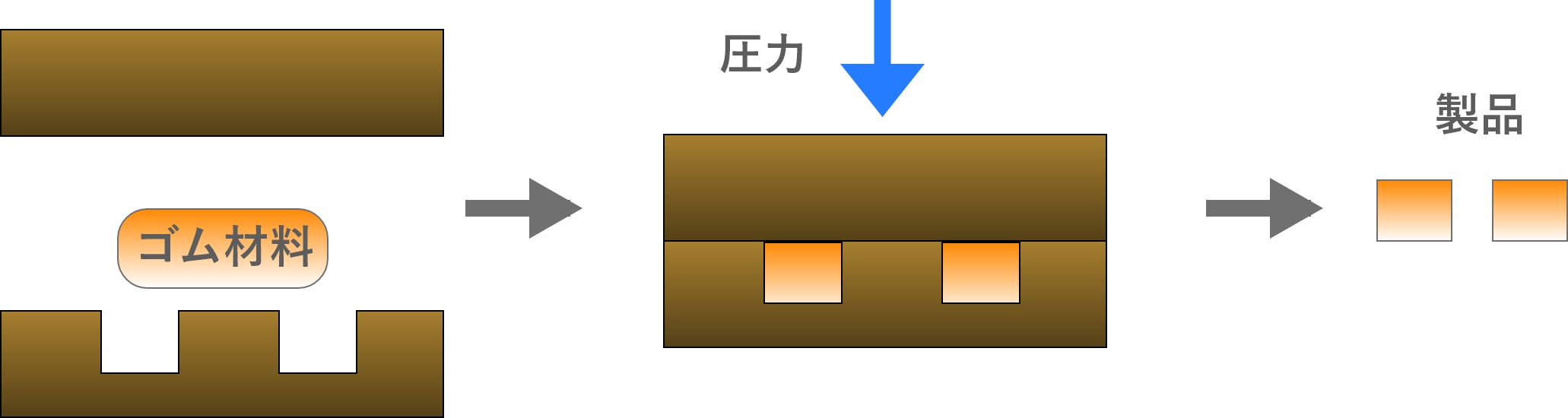
プレス成型は、上型と下型の間に生ゴム材料をセットし、そのまま挟んで製品形状に成型する方法です。金型の初期コストが安いですが、プレス前にゴム材料をある程度製品に近い形状にしておく必要がある点、作業の手間が少しかかります。 2~3cm程度の小さな製品であれば1度のプレスで多数の個数がとれるため、大量生産が可能です。 また、橋脚ゴムやビルの免震ゴムのような巨大なゴムの塊形状の場合は、プレス成型が用いられます。巨大なので、下記のトランスファーや射出成のように注入していたら時間がかかりすぎるためです。
トランスファー成形
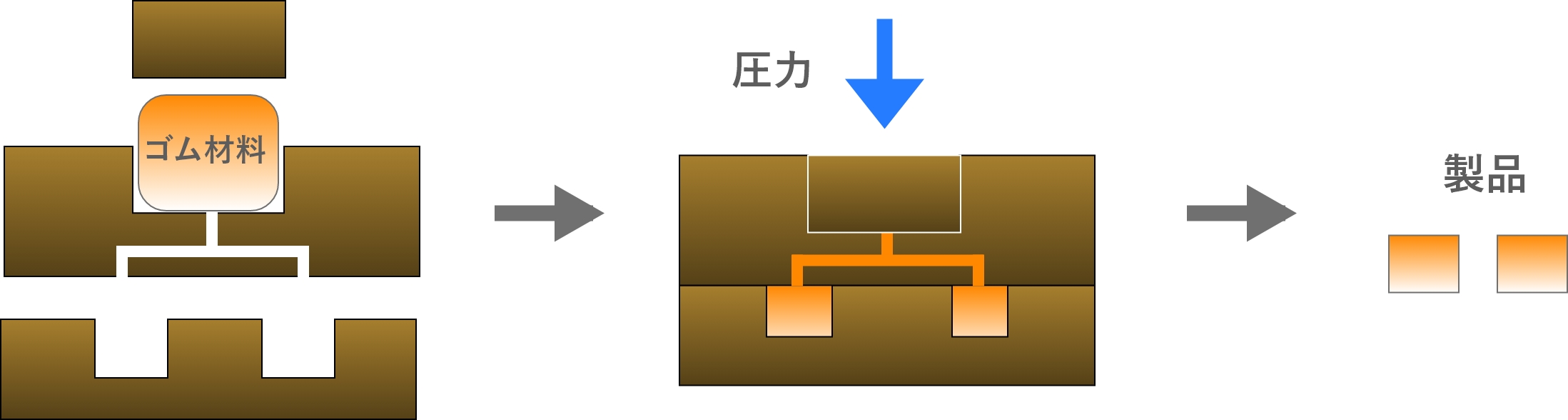
トランスファー成型は、上型にポットと呼ばれるゴム材料を置いておく部分があり、そこをプレスすることで製品部分に材料を注入し、製品を取り出す製造方法です。 プレス成型より金型費用はかかりますが、金属インサートが可能ですし、複雑な形状でもゴムが流れ込んで固まってくれるので作ることが出来ます。 ただし、材料を入れる手間がかかるため、大量生産には不向きで少量生産から中量生産に向いています。
射出(インジェクション)成形
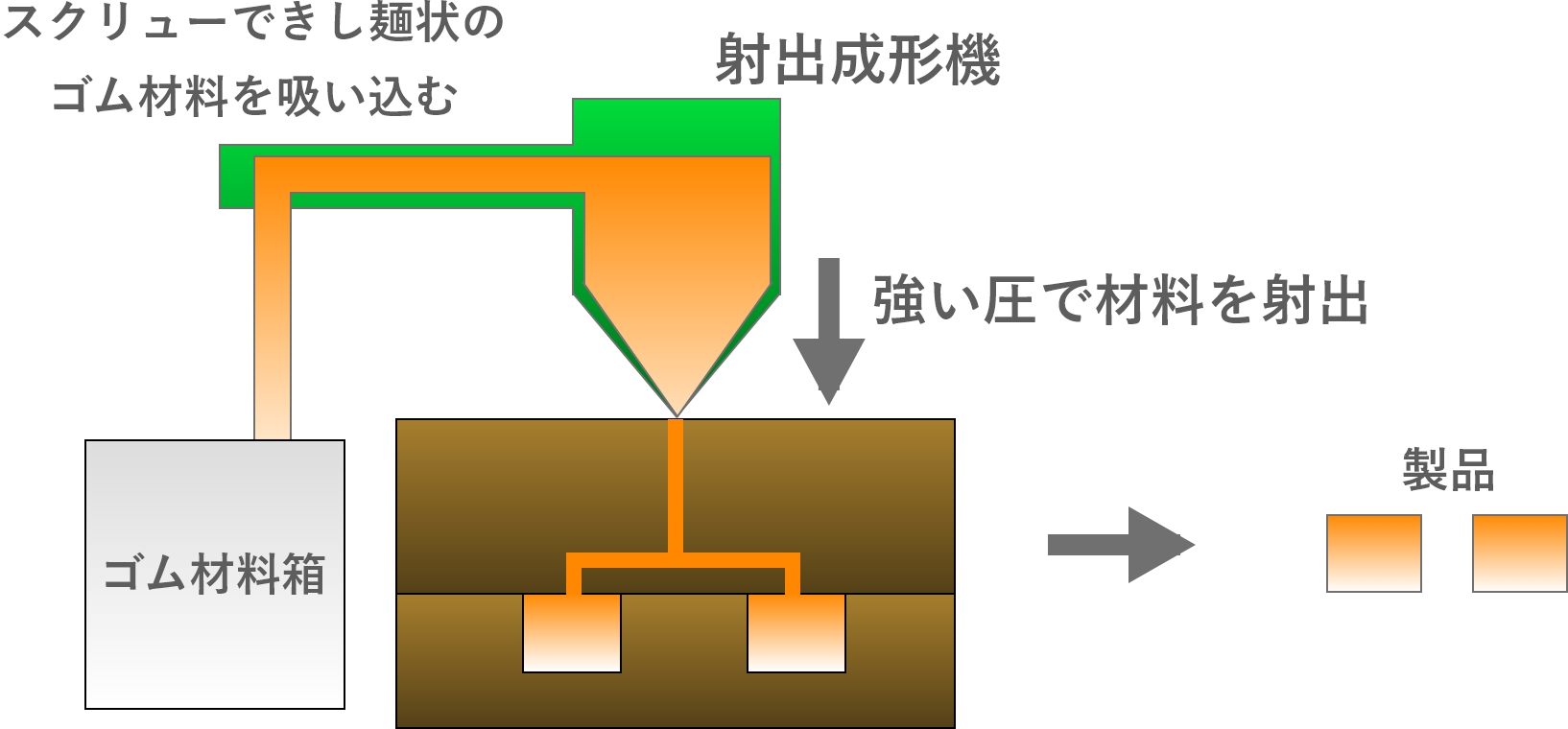
射出成型は、最も大量生産に向いた生産方法です。射出成型機という大きな注射器のような機械にスクリューがついており、そのスクリューに、きし麺状の長いひも状にしたゴム材料(通称リボン)を入れます。スクリューが板ガムを噛むように、クチャクチャとゴム材料を潰しながら吸い込み、液体状にして金型に注入します。 材料を入れる手間がなく、金属インサートも可能かつ、金型自体も大きく作ることが可能なため、一度のプレスで5~6個、小さめの製品なら20個ほど取り出すことが出来、非常に量産性の高い成型方法です。 その分、射出成型機や大型の金型など、設備が十分に整っている必要があります。
押出成形
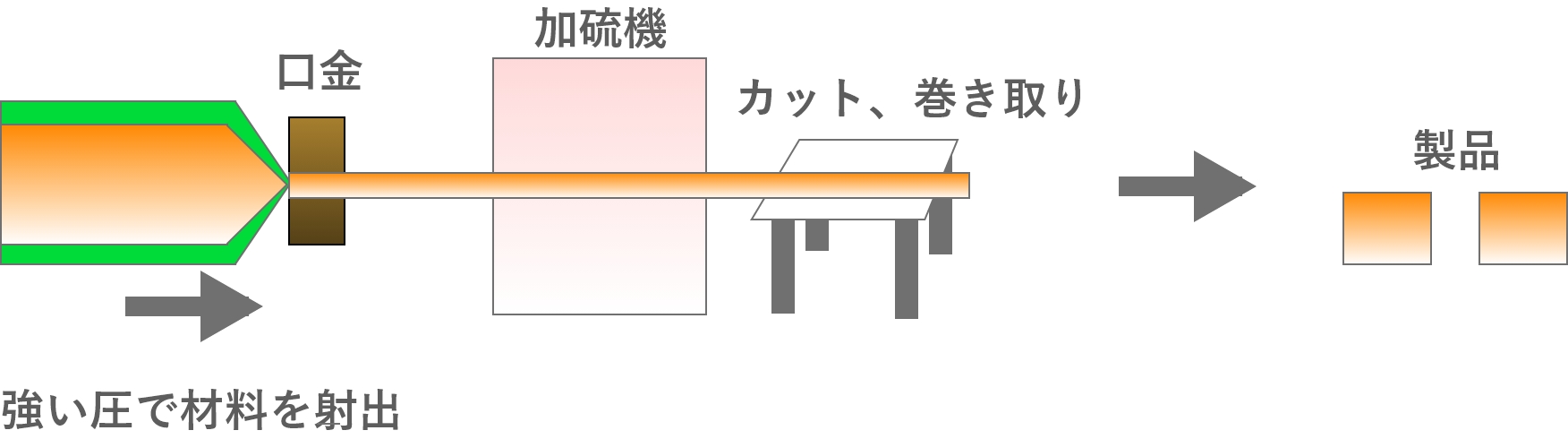
押出成形は、ところてんのようにゴム材料を金型内で加硫させながら口金を通して押し出すことで、長くて同じ形状の細長い製品を成形するのに適した、金太郎あめのような成型方法です。口金を変えることで様々な形状の製品を成形できます。パイプやチューブ、ホースなどを成形するのに適しており、量産性のある成型方法です。
金型成形品の製造事例
-
ブッシュ
-
ゴム成形品
-
ガスケット
-
ボタン
接着加工
接着にはゴム同士の接着、ゴムとプラスチック、ゴムと金属の接着があります。
ゴム同士の接着
ゴム同士の接着の場合には加硫接着が用いられます。 ゴムとゴムの間に柔らかくした生ゴムや加硫接着剤を仕込み、熱を加えることで化学結合させ、接着させます。
ゴムと金属の接着
ゴムと金属の接着にも、加硫接着剤が用いられます。金属を脱脂し、加硫接着剤の液を金属に塗り、ゴムと密着させた状態で加熱することで化学的に金属とゴムを接着させる加硫接着が用いられます。すでに完成品となったゴム製品と金属を接着させることはあまりなく、基本的にゴムの加硫時に、一緒に接着剤塗布済みの金具も金型内に入れて成形することがほとんどです。 金属の下処理が重要で、金属はあらかじめ化成処理やブラストをすることで表面を凸凹させ、ゴムと接着しやすい状態にする工程が大量生産の場合は必要です。
ライニング
ライニングとは基材の表面や内面を比較的厚い膜で覆う表面処理のことを言います。小野ゴム工業では、金属にゴムをライニングした製品を製造しています。ライニングも同様に、金属とゴムの加硫接着となります。
ゴムとプラスチックの接着
ゴムとプラスチックの場合、加硫温度(150度以上)まで上げるとプラスチック側が溶けてしまうため、接着材や接着テープが用いられることが多いですが、耐熱のプラスチックを使い加硫接着を行うこともあります。
塗装加工
天然ゴムやSBR、BR、NBRなどの化学的に二重結合があるゴムは紫外線や空気中のオゾンにより結合が切られ、劣化していきます。古い輪ゴムは伸びずに切れるのも、オゾン劣化です。 ゴムに伸縮性の塗装をすることで、日光やオゾンから守ることが出来ます。
性質が全く違う!把握すべきゴムの種類
強度 | 耐寒性 | 耐熱性 | 耐油性 | 体候性 | コスト | |
---|---|---|---|---|---|---|
NR (天然ゴム) |
||||||
BR (ブタジエンゴム) |
||||||
SBR (スチレンブタジエンゴム) |
||||||
NBR (アクリロニトリルゴム) |
||||||
ACM (アクリルゴム) |
||||||
Si (シリコンゴム) |
||||||
CR (クロロプレンゴム) |
||||||
EPDM (エチレンプロピレンゴム) |
||||||
FTK (フッ素ゴム) |
||||||
IIR (ブチルゴム) |
ゴム素材の中には200度以上の高温に耐えるもの、耐油性があるもの、耐寒性があるもの、機械的強度が強いもの、色々と特徴があり、ゴムの種類によって性質が全く違います。 そのため、必要に応じてゴムの種類(ポリマーの種類)を選ぶことが大切です。 例えば、タイヤに使われる天然ゴムは非常に機械的強度が高いのですが、オイルパッキンに天然ゴムを使ってしまったら、ドロドロと溶けてしまいます。 オイルシールに使うなら、耐油性のあるNBR、アクリルゴム、フッ素ゴムがおすすめです。 ただしNBRは100度以上の高温には適していません。
150度までの高温耐油環境ならばアクリルゴム、150度以上の高温耐油条件ならばシリコンゴム、200度以上ならばフッ素ゴム…
といったように、用途に応じてゴムの種類を選ぶことが大切です。 高温環境ではないのに、耐油性があるからとフッ素ゴムを採用することは無駄にコストがかかることに繋がります。常温ならばNBRで十分です。 一方、NBRを車のタイヤに使ってしまったら、すぐに摩耗してしまい使用不可能でしょう。タイヤや足回りの防振ゴムなど、強い荷重や力、摩擦が加わる部分には、機械的強度に優れる天然ゴムを使用せねばすぐに劣化してしまいます。 日光がよく当たる場所、強度も耐油性も求められない環境下ならば、EPDMが良いでしょう。分子構造中に二重結合がないので、劣化しにくく耐熱性も良いゴムです。 汚染性にも気をつけねばなりません。天然ゴムやNBRは二重結合があるので、日光やオゾンで劣化します。そのため老化防止剤やワックスなどの配合である程度は劣化を防止します。しかし、老化防止剤は汚染性が高く、触れたものに色移りしてしまうので、美観性が失われます。 EPDMやシリコンゴム、アクリルゴムやシリコンゴムなどには分子主鎖中に二重結合がないので、耐候性が優れており老化防止剤を必要としませんので、汚染性もありません。 また、同じEPDMでも、S-S結合の硫黄加硫の場合とC-C結合のパーオキサイド架橋の場合とでは、耐熱性や物性が大きく異なります。 このように、ゴムの種類によって全く性質が異なり、同じゴムの種類でもゴム配合によって性質を変えることが出来ます。 ゴム加工をする際は、最低でも用途とポリマーの種類は絶対に把握しておかなければなりません。
NR(天然ゴム)
天然ゴムは機械的強度が非常に高く、タイヤ、防振ゴム、免震ゴムなど、かなりの過重と力がかかる箇所に使用されます。 高温環境には弱く、耐候性に劣るため、老化防止剤やワックスなどの配合で補いますが、老化防止剤には色移りするなど汚染性が高いものが多く、外観品には使用出来ません。
BR(ブタジエンゴム)
非常に弾力が高く、良く跳ねるスーパーボールなどはBRで作られています。天然ゴムと混ぜて使うことで耐摩耗性が向上するため、タイヤや工業用ベルトなどに使用されます。
SBR(スチレンブタジエンゴム)
SBRは機械的強度が高いゴムです。天然ゴムと混ぜて使うことでさらに強度を上げることが出来、タイヤや工業用ベルトなどに使用されます。
NBR(アクリロニトリルゴム)
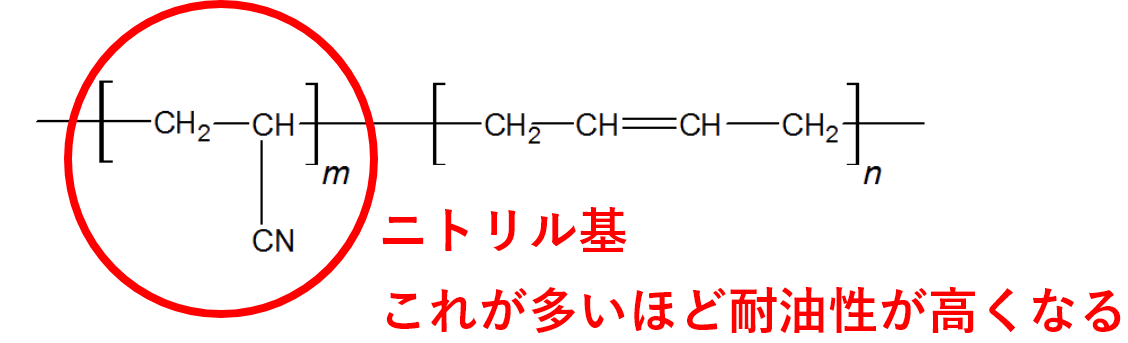
NBRは耐油性が強いゴムです。 水と同じで、分子構造中に極性(プラスとマイナスの電荷の偏り)を持つニトリル基があるため油をはじきます。 その代わり、耐寒性が落ち、-30度ほどの環境では脆くなってしまいます。可塑剤を入れて耐寒性を向上させることが可能です。 ニトリル部分が多いほど極性が高くなり、耐油性もあがりますが、その分ゴム自体が硬くなり、耐寒性が落ちてしまうトレードオフの関係となっています。 また、天然ゴムと同様に耐候性が劣るため、6Cなどの汚染性の高い老化防止剤を入れて使うため、外観品には使用が出来ません。 オイルパッキンなど油がかかる場所によく使用されます。
ニトリル基の量によって、極高ニトリル、高ニトリル、中高ニトリル、中ニトリル、低ニトリルの種類に分けられ、それぞれ使用用途によって使い分けられています。
ACM(アクリルゴム)
ACMもNBRと同様に耐油性があるゴムです。しかしNBRよりも高温に耐えることが出来ます。また、分子中に二重結合をもたないため、空気中のオゾン劣化がなく耐候性は良好です。
Si(シリコンゴム)
Siは、ACMがもっと高温に耐えられるようになったゴムというイメージです。ACM同様に耐候性は良好です。非常に安全性が高く、食品などにも用いることが出来、医療用にも適したゴムです。
CR(クロロプレンゴム)
CRはすべてにおいて、平均的なゴムです。汎用性が高く、何にでも使うことが出来ます。
EPDM(エチレンプロピレンゴム)
EPDMは、耐油性こそないものの、強度はそこそこ、耐熱性・耐候性も良好なため、汎用性の高いゴムです。耐候性が良好なので、汚染性の高い老化防止剤を入れる必要がなく、汚染性がありません。また非常によく伸びるゴムです。硬度が低いゴムであれば、700%近く伸びる材料もあります。主にハーネスグロメットや、電線の被覆材、など、多くのことに使われています。
FKM(フッ素ゴム)
フッ素ゴムはすべてにおいて優れているゴムなのですが、価格が非常に高いです。高温で耐油性も必要な、きわめて厳しい環境下で使われるゴムです。
IIR(ブチルゴム)
ブチルゴムは原材料の生ゴムの時点でかなり「ベチャッ」とした感じのゴムです。ベチャッとしているので衝撃吸収性に優れており、密封性にも優れています。 なので、空気が逃げないようなシール材、止水材に適しています。また、電線被覆材や防音材、防振材にも使用されます。
ゴムの加工不良と対策
ゴム加工において発生しやすい不良とその対策についてお伝えします。バリ不良
原因
成形加工時に、製品部分だけでなく上型と下型の隙間にもゴムが流れ込み必ずバリが発生します。そのバリが金型内に残ったまま次の製品を成形すると、バリが製品に挟まった状態で製品が出てきてしまいます。
また、成形だけでなく、切削加工時にも切削加工面にバリが発生します
対策
成形後、金型表面に張り付いたバリを払いのけ、エアーで吹き飛ばしてから次の製品を打ちます。また、金型内に仕込む材料が多すぎると、バリも大量に出来るため、出来るだけ材料の量を製品の大きさとジャストにして成形します。 また、製品のバリをとりやすいように、金型にはバリ溝を設けます
検査では、バリ不良がないかを全数目視検査します。
ヒケ
原因
ゴム素材の内部と外部の温度差で膨張率に差が生まれ、成形時に収縮することでヒケが生じます。 温度条件や気候条件でも発生します。
対策
型温、射出温度、射出速度など適切な成形条件を整えます。
材料としては、加工助剤の練りこみによりムーニー粘度を下げる、加硫遅延材やPG(ポリエチレングリコール)などの加硫促進剤などで加硫速度を調節します
気泡混入(エアー)
原因
成形時に、空気を巻き込んで製品を成形してしまう、あるいは材料に含まれる水分が、成形時に蒸発して気泡となります。
対策
バンピング(金型をプレスした直後、2~3回開け閉めして空気を逃がすこと)を行います。材料の射出速度や、温度などの成形条件を変更します。それでも難しければ、真空引きの設備を導入します。
ヤケ
原因
金型内をゴム材料が流れる途中に、一部が早期に加硫してしまい、異物混入したような形で製品が仕上がってしまいます。
対策
ゴム材料の射出温度、金型温度などの成形条件を見直します。
熱いところに放置されていた材料や使用期限切れの材料を使わない(先に加硫が進んでしまっているのでヤケやすい。材料管理をしっかりする)、また材料に加硫遅延材を入れるなどして対応します。
分散不良
原因
ゴム材料を練る際にカーボンやフィラー、硫黄や加硫促進剤がきちんと混ぜ込まれず、成形した際に異物として混入している
対策
ゴム練り機(バンバリーやニーダー)に入れる際に、材料を入れる順番や練り時間、温度を検討する。 ロールで加工する際は加硫材や促進剤を粉のまま入れるのでなく、予めポリマーに硫黄や促進剤が練りこんである原材料(マスターバッチ)の採用を検討する。 または、ストレーナーの採用も検討する
ゴム加工会社の選び方
ゴム加工の会社の選び方についてお伝えします。
最適な材料を提案してくれるか
使用用途に応じて、最適なゴムの種類を提案してくれる会社を選びましょう。 例えば、オイルシールパッキンを作りたい時に、 「材料はEPDMを検討しています。」 と伝えたら、 「EPDMだと耐油性がないので別の素材が適しています。」 と提案をしてくれる会社は、お客様の達成したい目的に寄り添ってくれると判断できます。
ゴム材料の扱いが丁寧か
真夏の暑い工場に、加硫材をすでに練りこんだ生ゴムがあると、金型に入れる前に加硫が進んでしまい、ヤケなどの不良をおこしてしまいます。 品質管理体制が整った会社に依頼をしましょう。
まとめ
ゴム加工には、切削加工・成形加工・接着(ライニング加工)・塗装があることについてお伝えしました。 切削は少量生産、成形は大量生産に向いた加工法です。 また、形を作るだけでなく、ゴムの種類が使用用途に適した性質のものかを知っておく必要があります。 ゴムの種類も色々ありますので、是非参考にして、検討してください。 小野ゴム工業は100年の実績と、豊富な知識で、お客様の求めるゴム製品を実現します。 ゴムのことならお気軽にお問い合わせください。小野ゴム工業ではゴムの加工・成型に多くのノウハウや実績を
持っています。加工のご依頼やゴム加工の相談は下記よりお問い合わせください。